Laser cutting in medical device manufacturing is commonly used because of its effectiveness, precision, and versatility. Medical device manufacturers widely utilize laser-cutting machines to accurately fabricate complex components and devices. These technologies precisely shape and customize medical equipment to meet individual patient needs, using a focused laser beam to cut through various materials, including metals, polymers, and ceramics. The manufacturing process often incorporates laser engraving to imprint medical equipment with permanent identifiers and markings, ensuring traceability and compliance with regulatory standards.
Laser cutting is instrumental in producing medical devices such as valve frames, flexible shafts, vascular clips, and cardiac stents. Its capability to create intricate components with tight tolerances makes laser cutting ideal for generating complex geometries and features required in medical devices. It is employed to precisely cut materials to prevent deformation during manufacturing processes and to accurately cut tubes used in catheters and other medical devices.
The precision and consistency of laser cutting are critical for the production of medical devices, enhancing the quality, safety, and efficacy of the devices. The manufacturing industry can produce medical equipment and components consistently and reliably using laser cutting, ensuring adherence to stringent regulatory standards and meeting the needs of patients and healthcare professionals. Laser cutting enables medical device designers to innovate and customize, facilitating the development of groundbreaking solutions to address various medical challenges.
Laser cutting, powered by advanced laser cutter technology, offers several advantages to the medical manufacturing industry, such as high precision, quick turnaround times, cost-effectiveness, and versatility in material processing. Medical device manufacturers leverage laser cutting technology to optimize manufacturing processes, enhance productivity, and maintain high-quality standards while producing medical items. Benefits such as customized output, reduced material waste, and improved safety features make laser cutting a preferred choice for medical device manufacturing in today’s demanding healthcare environment.
Why Are Laser Cutting Machines Used to Make Medical Devices and Components?
Laser-cutting machines are employed in creating medical components and devices due to their numerous advantages. They offer exceptional precision, crucial for surgical procedures and a significant benefit. Laser technology facilitates surgical precision and reduces recovery times for patients by enabling physicians to make precise incisions. These devices are vital for manufacturing a variety of medical instruments, including vascular clips, flexible shafts, valve frames, stents, and bones. The uninterrupted cutting process of laser technology ensures a stable torque response during surgical procedures.
Another advantage is the rapid turnaround times provided by laser-cutting equipment. Their swift manufacturing capability shortens lead times and enhances the efficiency of surgical procedures, thereby increasing the profitability of medical clinics. The precision and low power consumption of laser engraving technology contribute to its widespread use in medical device manufacturing, making it cost-effective.
Customization is a key feature of laser-cut technology, allowing for the creation of instruments tailored to specific clinical needs. Unlike traditional coiling and braiding methods, laser cutting can produce tools with the required stiffness and flexibility. These machines are compatible with various materials, including plastic, metal, and glass, which reduces the need for multiple tools and saves costs.
Laser cutters ensure that catheters are manufactured without flattening or misshaping, preserving the integrity of the final product as it navigates through a patient’s anatomy. The growing demand for medical equipment underscores the critical need for increased capacity. Laser-cutting machines enable manufacturers to advance their technology and boost productivity, ensuring that patients receive medical treatments promptly. This supports providers by enhancing operational efficiency and meeting the rising healthcare demands caused by population growth and aging demographics.
What are the Standards for Medical Devices?
The standards for medical devices are listed below.
- ISO 14971: Risk Management: This standard addresses the detection and management of hazards associated with medical devices throughout their lifespan. Medical device manufacturers must implement risk management processes, such as identifying potential risks, assessing risks, and implementing risk control measures. International sales of medical equipment require adherence to ISO 14971.
- ISO 10993: Biocompatibility: This standard covers the biocompatibility of medical devices, ensuring they do not cause adverse reactions when in contact with patients. It provides guidelines for evaluating the biological safety of medical devices based on the type of device, material, intended use, and duration of patient contact. The standard aims to protect healthcare professionals and patients from adverse outcomes.
- IEC 62304: Medical Device Software: This standard focuses exclusively on the development and maintenance of software used in medical devices. It specifies requirements for the safe design, development, production, and maintenance of medical device software, including software integrated into or used as a medical device.
- ISO 9001: Quality Management: ISO 9001 is a general quality management standard applicable to various sectors, including medical device manufacturing. It supports regulatory compliance, enhances accountability, and helps companies establish quality management procedures. ISO 9001 promotes continuous improvement and provides a framework for maintaining product quality and customer satisfaction.
- ISO 13485: Quality Management for Medical Devices: This standard, building on the foundation set by ISO 9001, is specifically designed for medical device manufacturers. It emphasizes quality control, traceability, regulatory compliance, and risk management in the manufacturing of medical devices. Compliance with ISO 13485 boosts operational efficiency and opens new markets.
- ISO 14001: Environmental Management: This standard focuses on environmental management systems, helping businesses reduce waste, conserve energy, and minimize their environmental impact. ISO 14001 standards assist medical device manufacturers in saving costs, complying with regulations, and improving sustainability.
- ISO 50001: Energy Management: Standardizing energy management practices enables businesses to reduce operational costs and enhance energy efficiency. This standard is beneficial for medical device manufacturers seeking to improve their environmental performance and supports ISO 14001 standards.
- OHSAS 18001: Occupational Health and Safety / ISO 45001: These standards help companies identify and mitigate workplace hazards by defining requirements for occupational health and safety management systems. Ensuring worker safety is crucial in the medical device industry, and adherence to these standards increases accountability and reduces risks.
- ISO 27001: Information Security: ISO 27001 addresses information security management, crucial as medical devices become more connected and vulnerable to cyber-attacks. It provides guidelines for identifying and managing cybersecurity risks, protecting private information, and ensuring continuity of operations even during a breach.
How Does Laser Cutting Enable Standards for Medical Device Manufacturing?
Laser cutting enables standards for medical device manufacturing by providing a precise and adaptable method for producing parts and devices. Utilizing a concentrated beam of light, laser cutting precisely and consistently cuts through materials. This technique is effectively employed to manufacture complex parts and components for medical devices.
The benefits of laser technology in production include its high accuracy, rapid turnaround times, and cost-effectiveness. Laser-cutting tools are compatible with metals, plastics, and ceramics, which are commonly used materials in medical device manufacturing. They offer exceptional control over the cutting process, allowing for the creation of complex geometries and intricate patterns with minimal material waste.
Compared to other standards in medical device production, laser cutting excels by enabling manufacturers to create parts with the precision required to meet stringent quality standards. It ensures accuracy and consistency, essential for maintaining the integrity and functionality of medical devices, whether they are sophisticated surgical instruments or components for implantable devices.
Laser cutting technology’s customization capability simplifies the production of specialized parts for individual patients’ conditions. This adaptability allows manufacturers to meet the specific needs of patients and healthcare professionals, aligning with the increasing demand for personalized medical treatments and technologies.
Furthermore, laser cutting supports the application of risk management practices outlined in standards like ISO 14971 by offering precise control over the production process. This precision helps reduce the likelihood of defects or irregularities in medical device components, thereby enhancing the overall safety and reliability of the products.
What Are Some Applications of Laser Cutting for Medical Device Manufacturing?
Some applications of laser cutting for medical device manufacturing include:
- Cardiac Stents: Mesh tubes used to treat atherosclerosis and coronary artery blockages. These stents are precisely fabricated from metal materials thanks to laser cutting technology.
- Vascular Stents: Similar to cardiac stents, these devices are used to address various vascular issues. The precise cutting of materials, made possible by laser cutting, ensures their excellent performance and compatibility.
- Precision Tubes: Widely utilized in medical applications, precision tubes are essential components of numerous tools and devices in medicine, cut using laser-cutting technology.
- Vascular Clamps: Used to temporarily block blood vessels during surgical operations, these devices are manufactured with laser cutting equipment. The precision and accuracy provided by laser cutting ensure the reliability of these critical devices.
- Valve Frames: Components of artificial heart valves, valve frames are more easily constructed with laser cutting technology. Strict cutting and shaping are required for these frames to ensure optimal functionality within the body.
- Bone Reamers: Surgical devices that enlarge bone cavities during orthopedic treatments. Laser cutting enables the production of bone reamers with refined edges and complex patterns, essential for precise bone preparation.
- Honing Heads: Manufactured by laser cutting machines, these tools are utilized in various medical procedures to smooth out cavities or surfaces. The precision of laser cutting ensures the uniformity and accuracy of honing heads.
- Flexible Shafts: Essential parts of endoscopes, catheters, and other medical equipment, flexible shafts require complex geometries and precise dimensions. Laser cutting technology fabricates flexible shafts, ensuring their durability and flexibility.
These applications highlight the versatility and precision of laser cutting in medical device manufacturing, enabling the production of intricate and highly specialized components necessary for modern medical treatments.
What is the Importance of Laser Cutting for Medical Device Manufacturing?
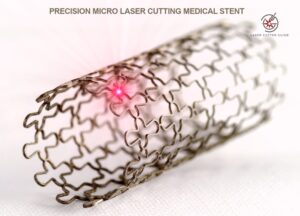
The importance of laser cutting in the manufacturing of medical devices lies in its crucial role in achieving the precision, complexity, and quality required for modern medical equipment. Laser technology has revolutionized the manufacturing process by offering unparalleled levels of precision and flexibility, essential for producing products that meet the stringent standards of the healthcare industry.
Laser cutting facilitates the production of complex components with micron-level precision, a primary advantage. Precision is vital for medical devices, as even minor errors can significantly impact patient safety and device effectiveness. Laser cutting technology allows manufacturers to create complex patterns and geometries with exceptional precision, ensuring devices function as intended within the human body.
The intricacy of many medical devices makes laser cutting an ideal manufacturing process. Its versatility enables the creation of complex patterns on catheters or precise cutting of components for implantable devices. This capability is crucial for meeting the design and functional requirements of everything from minimally invasive surgical instruments to sophisticated implanted devices.
Laser cutting yields components of superior quality compared to traditional manufacturing methods. By producing precise, clean cuts with minimal material waste, laser technology ensures the final products are of exceptional quality. This is critical for medical devices, where consistency and reliability are paramount. By ensuring the integrity of each component, laser cutting enhances the overall safety and functionality of medical devices, benefiting patients and healthcare professionals alike.
Laser cutting keeps manufacturers at the forefront of medical device innovation. The advancement of medical technology has placed increasing demands on production processes. The flexibility and precision offered by laser technology allow designers to keep pace with evolving regulations and industry standards. By employing laser cutting, medical device manufacturers can push the boundaries and improve patient outcomes.
What are the Benefits of Laser Cutting for Medical Manufacturing?
The benefits of laser cutting for medical manufacturing include:
- Safety: Laser cutting is inherently safe, as it does not involve physical contact between the processing tool and the material, thanks to the laser being enclosed within a protective glass tube. This feature reduces the risk of accidents or injuries, promoting a safer work environment for employees.
- Cost-effectiveness: Compared to other manufacturing techniques, laser machines are more cost-effective due to their use of inexpensive components. This affordability makes laser cutting a viable option for medical device manufacturers looking to reduce production costs while upholding quality standards.
- Material Versatility: Laser technology is compatible with a variety of materials used in medical device production, including glass, metal, and plastic. This adaptability allows manufacturers to meet diverse design requirements and preferences.
- Energy Efficiency: Due to their low power consumption and maintenance needs, laser cutters are energy-efficient, contributing to the overall sustainability of medical manufacturing facilities and reducing operational costs.
- Precision: The precision of laser cutting technology is unmatched, crucial for medical products that often include small parts and complex designs. This precision ensures the quality and functionality of the finished products by allowing the production of delicate and intricate components with high accuracy.
- Regulatory Compliance: The medical industry is highly regulated, requiring adherence to stringent quality and safety standards. The precise control over the manufacturing process provided by laser technology simplifies compliance, ensuring consistency and reliability in the production of medical devices. Compliance is vital for maintaining the trust and confidence of healthcare professionals and regulatory bodies, underscoring the importance of laser cutting in ensuring medical devices meet strict regulations, thereby enhancing patient safety and device efficacy.
What are the Challenges of Laser Cutting for Medical Manufacturing?
The challenges of laser cutting for medical manufacturing include:
- Material Compatibility: Not all materials used in medical device manufacturing are suitable for laser cutting. Certain polymers or ceramics may be difficult to cut or yield undesirable results when processed with a laser. Manufacturers must carefully assess material compatibility and select appropriate laser parameters to ensure high-quality outcomes.
- Thermal Damage: The heat generated by laser cutting can cause thermal damage to the processed material. This is crucial for components requiring tight dimensional tolerances or made from sensitive materials. Managing heat input and minimizing thermal effects are essential for preserving the integrity of medical devices and preventing damage.
- Cost of Equipment and Maintenance: The initial purchase and ongoing maintenance of laser cutting equipment are expensive; regular servicing and calibration are necessary to ensure optimal performance. The cost of laser consumables, such as gases and lenses, further increases the total operational cost. Manufacturers must consider these expenses when integrating laser cutting technology into their production processes.
- Programming Complexity: Laser cutting requires intricate programming to determine cutting paths, power levels, and other parameters. Errors in programming or inefficiencies can lead to production delays or suboptimal cutting results. Skilled personnel with specialized knowledge in laser programming and operation are essential for overcoming these challenges and optimizing manufacturing processes.
- Safety Concerns: The use of high-intensity laser beams in cutting poses risks to workers if adequate safety measures are not in place. Exposure to laser radiation or accidental contact with moving parts can lead to health risks or injuries. Implementing robust safety protocols and providing comprehensive training for employees are necessary to ensure a safe working environment.
- Regulatory Compliance: The laser cutting process in medical manufacturing is governed by strict standards regulating the production of medical devices. Manufacturers must demonstrate the efficacy, safety, and quality of laser-cut components through extensive testing and documentation. Navigating regulatory compliance adds administrative complexity and obligations to the manufacturing process, highlighting one of the significant challenges of laser cutting in the medical manufacturing industry, as adhering to regulatory norms complicates the production process and increases administrative burdens.
What Are the Other Industrial Applications of Laser Cutting?
The other industrial applications of laser cutting span a wide range of industries and specialized tasks beyond conventional production methods. One significant application is laser marking for branding. Laser marking offers a precise and durable method for industries to apply logos, serial numbers, barcodes, and other identifiers onto their products. This process creates a high-quality mark on the surface of the workpiece by selectively removing material or changing its appearance with a laser beam. The excellent resolution and contrast make laser marking ideal for producing fine marks and intricate patterns on various materials, such as glass, ceramics, metals, and plastics. Due to its speed, durability, flexibility, and advantages in enhancing product traceability and brand recognition, laser marking is a favored choice for branding applications across different industrial sectors.
Laser welding is another crucial application of laser cutting in the industrial sector, particularly in the manufacturing of surgical instruments and systems. Laser welding offers several advantages over traditional welding techniques, including minimal thermal distortion, speed, and precision. In the medical industry, where quality and precision are paramount, laser welding is vital for creating intricate and delicate parts for surgical tools, implants, and medical equipment. By fusing different materials, such as metals and polymers, with minimal heat-affected zones, laser welding ensures the integrity and performance of the final product. This technique facilitates the production of medical devices that are biocompatible and hermetically sealed, meeting strict regulatory standards and ensuring patient safety. Extensively used in industrial sectors for a variety of applications, including consumer products, electronics, automotive, and aerospace, laser welding is valued for its ability to produce precise and clean welds.
In addition to conventional cutting and shaping, the industrial applications of laser cutting include specialized techniques like marking and welding. Laser cutting technology continues to lead innovation and evolution in the manufacturing industry, offering versatile solutions for challenging fabrication issues. By enhancing productivity, quality, and accuracy across various industrial sectors, laser cutting is utilized to add branding elements to products or create intricate welds on surgical equipment.
What Are the Laser Types Used for Medical Device Manufacturing?
The laser types used for medical device manufacturing include:
- Fiber Lasers: Widely employed for medical device manufacturing due to their reliability, low power usage, and highly accurate beam. They are commonly used in cutting, welding, and marking applications, particularly when working with metal parts for implants, surgical tools, and other medical equipment.
- CO2 Lasers: Favored for their ability to cut through a diverse range of materials, including metals, plastics, and biological materials. They are frequently utilized for cutting and engraving tasks in medical device production, such as crafting complex patterns on surgical instruments or applying identification labels on medical equipment.
- Nd:YAG Lasers: Known for their high-power outputs and precise control, neodymium-doped yttrium aluminum garnet lasers are ideal for welding and cutting tasks in the medical device manufacturing industry. They are often employed in welding titanium and stainless steel components, crucial for constructing surgical equipment and implants.
- Excimer Lasers: Employed extensively in medical device manufacturing for precise material removal. Producing ultraviolet light with a short wavelength, they are suited for tasks requiring extreme precision and minimal heat-affected zones, such as ablating materials for microfluidic devices or drilling tiny holes in stents.
- Diode Lasers: Valued for their compact size, high efficiency, and precise control, making them suitable for a variety of medical device manufacturing applications. They are often used for cutting, welding, and marking tasks, especially where space limitations or mobility are critical factors. This demonstrates the adaptability of laser types in meeting specific production needs in the medical device sector, where precision and compactness are key.
Is Laser Cutting More Precise than Machining for Medical Devices?
No, laser cutting is not necessarily more precise than machining for medical devices. Although laser cutting achieves high precision and accuracy, machining processes such as milling and turning can achieve similar or even greater precision in certain cases.
The method of cutting plays a part in this. Laser cutting uses a concentrated beam to evaporate or melt the material, introducing thermal distortion, especially with thicker or more conductive materials. This can result in slight deviations from the intended dimensions and geometries, affecting the overall accuracy of the final product.
Machining, on the other hand, uses cutting tools to remove material from a workpiece, offering precise control over the cutting path and depth. With the appropriate tools and machining conditions, manufacturers can achieve tight tolerances and surface finishes that are challenging to replicate with laser cutting alone.
Machining offers greater versatility regarding the materials it can process. While laser cutting is optimal for thin materials like sheet metal or plastics, machining can handle metals, ceramics, and composites, allowing manufacturers to select the best material for their application without compromising accuracy.
Specialized machining techniques are used for complex assemblies and critical components of medical devices. Advanced tool paths and machining methods implemented by computer-controlled machining centers ensure accuracy and consistency across large production runs.
Although laser cutting is a vital technique in medical device manufacturing, particularly for applications requiring complex patterns or fine details, the choice between laser cutting and machining depends on various factors, including material, design complexity, production volume, and desired outcome. Each method has its strengths and weaknesses, and manufacturers leverage the unique qualities of each process to produce the precise and high-quality medical devices needed for contemporary healthcare applications.
Does Laser Manufacturing of Medical Devices Cost More Than Traditional Manufacturing?
Yes, laser manufacturing of medical devices costs more than traditional manufacturing. Laser technology offers numerous benefits, such as increased precision, flexibility, and efficiency, but it incurs higher start-up and ongoing costs compared to older manufacturing methods.
The initial investment required to acquire and set up laser-cutting equipment significantly contributes to the higher cost of laser manufacturing. Significant financial investments are necessary for the complex and sophisticated machinery that comprises laser-cutting systems. The enhanced features and capabilities needed to precisely process medical-grade materials result in a higher price tag for specialized laser systems designed to manufacture medical devices.
Laser production also demands ongoing maintenance and operating expenses, which accumulate over time. Regular service, calibration, and replacement of consumable components, such as lenses and gases, are necessary to maintain optimal performance and reliability of laser cutting equipment. These maintenance costs can add up, especially in high-production environments or for specialized medical device applications where strict quality control protocols are required.
Furthermore, the cost of materials is higher for laser production than for conventional manufacturing methods. Laser cutting methods, known for their higher precision and reduced material waste, necessitate the use of more expensive materials to minimize losses. Specialized materials for laser cutting, such as medical-grade metals or polymers, are costlier than standard materials used in traditional manufacturing processes.
The complexity of the actual manufacturing process is another factor that drives up the cost of laser manufacturing. Successfully programming and operating laser cutting equipment requires workers with specific training and expertise. The labor costs for employing highly skilled workers increase the overall expenses of laser manufacturing, particularly when compared to traditional production techniques that require less specialized training.
Can Laser Cutting and Laser Engraving Be Used Together in Manufacturing Medical Devices?
Yes, laser cutting and engraving can be combined in the manufacture of medical devices. Laser engraving is a complementary process that adds identifying markings, logos, serial numbers, and other essential information to the surface of components, typically created by precision cutting materials for medical devices.
Laser engraving serves several purposes for medical devices. Firstly, it permanently marks medical equipment with critical information necessary for identification, tracking, and regulatory compliance. By directly etching unique identifiers, such as lot codes or serial numbers, onto component surfaces, manufacturers can trace the production history of each item and ensure quality control. This capability facilitates recalls when necessary.
Furthermore, laser engraving brands and customizes medical equipment to meet specific consumer demands or market preferences. By adding logos, product names, or instructional markings, manufacturers enhance the visual appeal and brand recognition of medical devices. The ability to customize is advantageous for medical devices used in consumer-facing applications or niche healthcare markets where branding and distinctiveness are key factors.
Laser engraving offers greater precision, consistency, and durability than traditional marking techniques, such as etching or stamping. High-resolution marks with fine details and sharp edges, produced by laser engraving equipment, ensure legibility and mark longevity, even under abrasive conditions or sterilization processes. This level of accuracy and robustness is crucial for medical devices used in long-term patient care or surgical procedures, where precision and reliability are paramount.
By integrating laser engraving and cutting, manufacturers can produce medical devices with enhanced flexibility, efficiency, and quality control. The seamless integration of cutting and engraving operations via a laser engraving machine streamlines the manufacturing workflow and eliminates the need for additional post-processing steps. Laser engraving thus becomes a valuable tool in the healthcare sector’s production arsenal, improving the functionality, safety, and branding of medical products.