Our Latest Posts
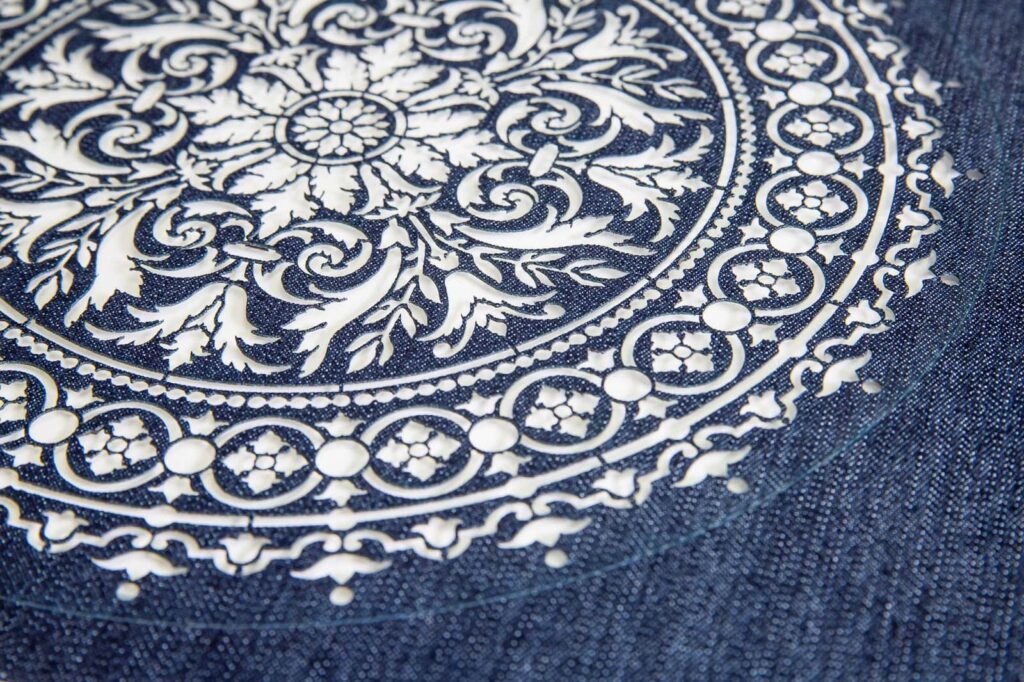
7 Disadvantages of using Laser Cutting for making stencils
Using a laser cutter to produce stencils has, in theory, a few disadvantages. Usually, laser cutting is very fast, accurate, and overall a very good tool. It offers a high degree of repeatability and automatization. However, there are some minor disadvantages when it comes to laser cutting stencils that have to be kept in mind. Firstly, one needs a certain degree of expertise to successfully laser-cut any material. It requires some trial and error as well as practice. Secondly, many laser cutters are quite costly, especially when they must be able to cut through thick metal sheets. Thirdly, plastics have the potential to release harmful gases when laser-cut for the stencils. Therefore, it is very important to check the safety data sheet of the material that must be laser-cut. One must have sufficient airflow and a venting system installed with the laser cutter. 1. Multiple stencils are required for multilayered
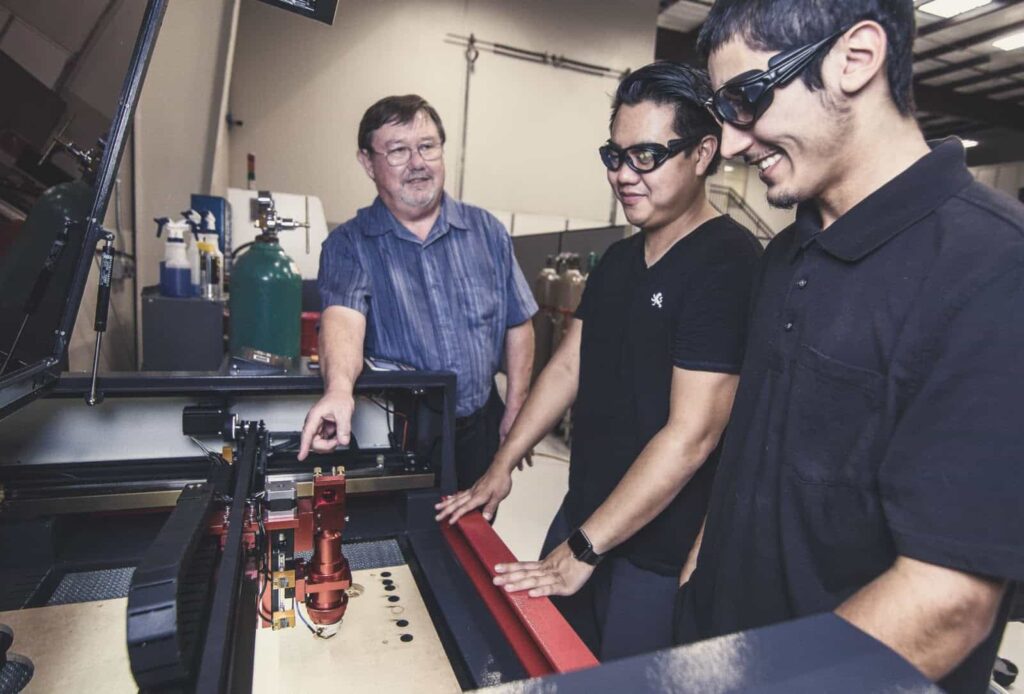
6 Uses of Laser Cutting and its Importance
Laser cutting is a flexible and accurate cutting method with various applications across multiple sectors. Its significance lies in its precision and adaptability, enabling the creation of elaborate and complex designs with exceptional precision and speed. Laser cutting has transformed numerous sectors by facilitating the development of new products and enhancing existing ones. Its ability to work with a wide range of materials and produce clean, accurate cuts has established it as an essential tool in manufacturing, design, and other industries. Laser cutting can be applied to nearly every material, whether it be metal, ceramics, wood, or plastic. The process involves directing a high-power laser beam onto a surface, which then evaporates, burns, or melts the material. The precision of a laser cutter is remarkable, capable of positioning with 10 µm accuracy, making it a vital tool in various industries. Below are the six uses of laser cutting: Laser Cutting
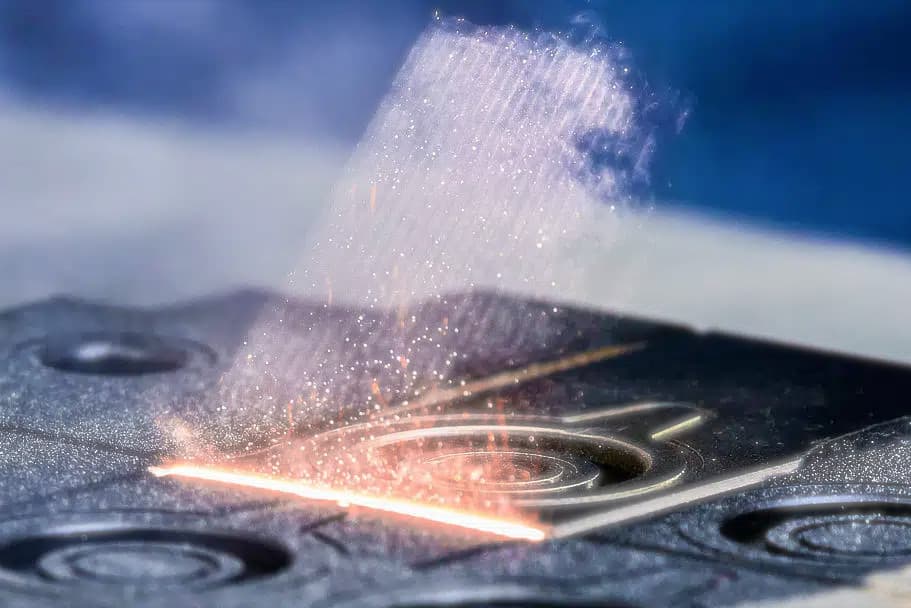
Laser Vaporization Cutting: Definition, Advantage, and Disadvantages
Laser Vaporization Cutting is a special form of laser cutting. It is a particular technology that uses a very strong laser beam that hits the surface of the workpiece. The laser beam rapidly heats the top surface layer. The material evaporates as the temperature rises over its boiling point. The laser beam’s high energy allows evaporation before the substance melts. Laser vaporization cutting is mostly used for thin plates of metal, paper, wood, or plastic. Moreover, laser vaporization and laser fusion cutting are similar processes. However, they are not exactly the same. Laser vaporization, or laser ablation, is often used for tasks such as micromachining, cleaning the surface, and laser drilling. On the other hand, laser fusion cutting is the process where the laser beam is pointed directly at the material, which quickly heats up and melts. A high-pressure gas jet blows the melting material away, creating a clean incision.